November 2013: Neuer Zeitraffer-Test auf Hapag-Lloyd Flaggschiff
Im Sommer 2013 haben wir zeitgleich zwei neue Tests begonnen. Die beiden gleich bestückten Rahmen tragen jeweils 10 Testbleche mit neuen unterschiedlichen Wachs-Mischungen. Der erste Rahmen wurde auf unserem Testturm auf Helgoland angebracht, der zweite Rahmen in einem Containerschiff. Wie immer bei unseren Prüfungen treten die Wachs-Produkte gegen ein Referenzprodukt an, von dem wir wissen, dass es hervorragend funktioniert. Dieses Mal war es unser Rostschutz-Fett TimeMAX 1500 RESCUE WAX. Das Material ist eine Mischung aus den beiden Fettprodukten TimeMAX 1000 und TimeMAX 2000. Mit diesen beiden, damals in Kombination angewendeten, Produkten hatten wir bei dem Langzeittest der großen Autozeitschrift “Oldtimer Markt” mehrfach den ersten Platz belegt (siehe z. B. Ausgabe September 2012).
Ziel unser aktuellen Prüfungen ist die Entwicklung eines neuen Rostschutz-Sprays für den Hohlraum- und Unterbodenschutz bei Fahrzeugen. Ein weiterer Test mit den Wachsprodukten beginnt im Dezember auf Helgoland. Hier werden dann keine Prüfbleche, sondern Hohlkörper aus Blech verwenden. Das Wachs-Spray wird erst auf den Markt gebracht, wenn es alle Tests bestanden hat. Wie immer lassen wir uns bei der Entwicklung Zeit!
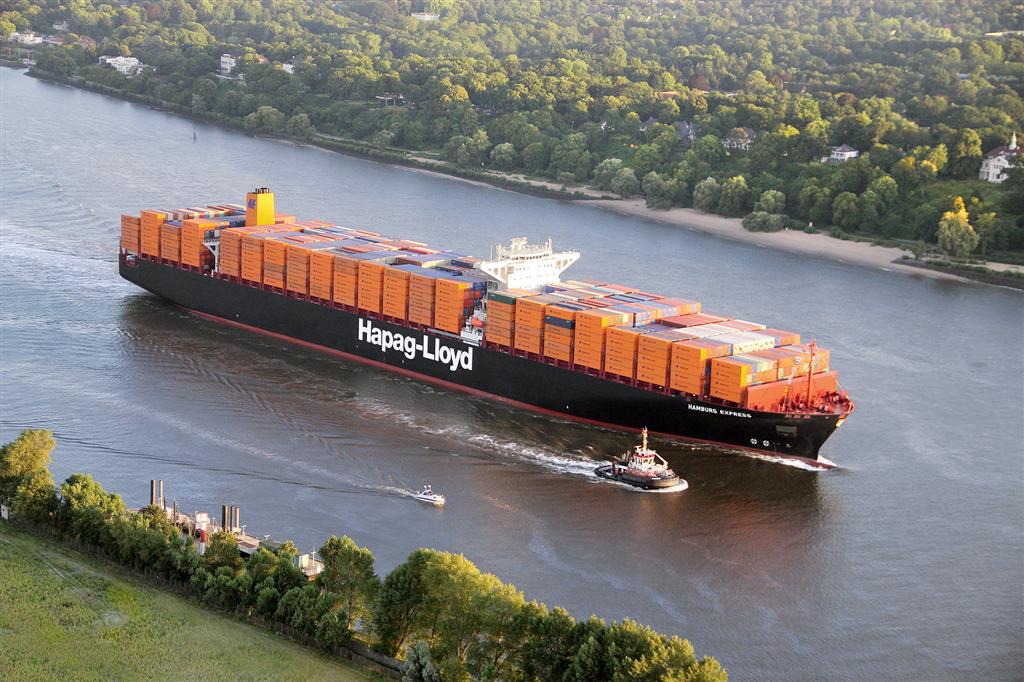
Auf dem Containerschiff testen wir die neuen Wachsprodukte von TimeMAX unter extremen Bedingungen. Der Rahmen mit unseren Testbleche hängt in den mit Salzwasser gefüllten Ballastwassertanks.
Die Presseabteilung von Hapag-Lloyd in Hamburg hat eine sehr interessante 17 Seiten lange Broschüre über den Bau des riesigen Schiffes zusammengestellt. Der Bau des Schiffes in einer koreanischen Werft hat von der Kiel-Legung bis zur Fertigstellung nur 283 Tage gedauert. Das Besondere: Das PDF Dokument zeigt die Herstellung als Fotogeschichte mit einem Countdown vom ersten bis zum letzten Tag. Hier der Link zur Internetseite von Hapag-Lloyd:
http://www.hapag-lloyd.de/downloads/press_and_media/publications/Broschure_Schiffsneubauten_engl.pdf
Auf einigen Fotos auf den Seiten 2, 4 und 6 kann man die Ballastwassertanks hinter der Außenhaut sehr gut erkennen.
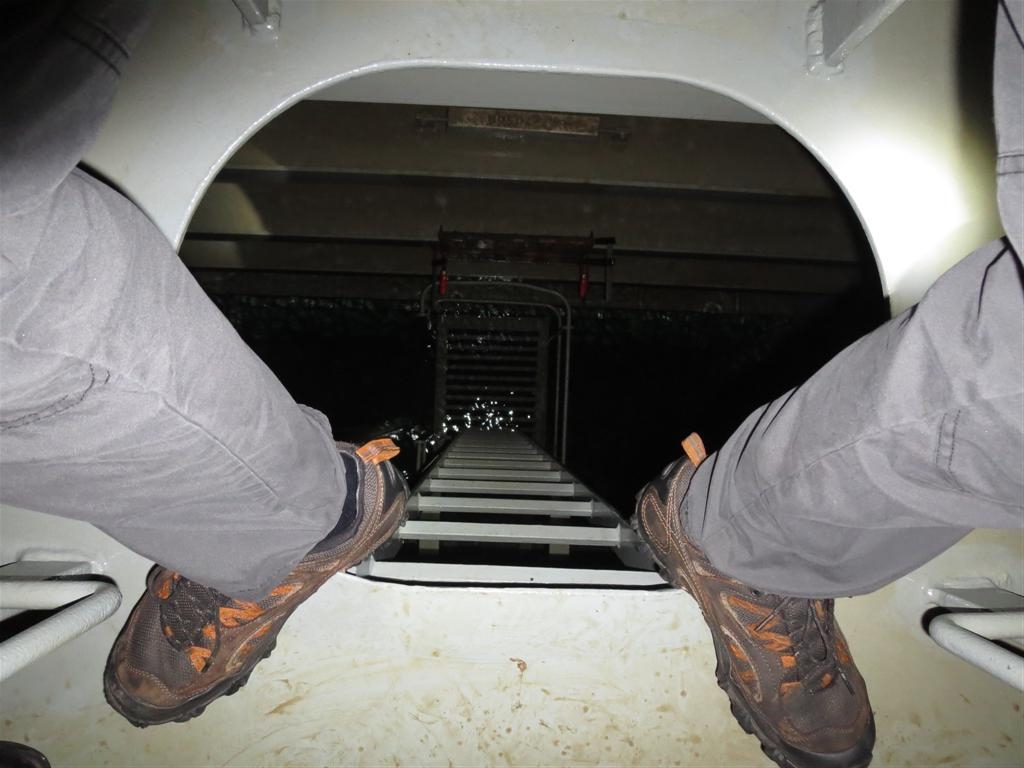
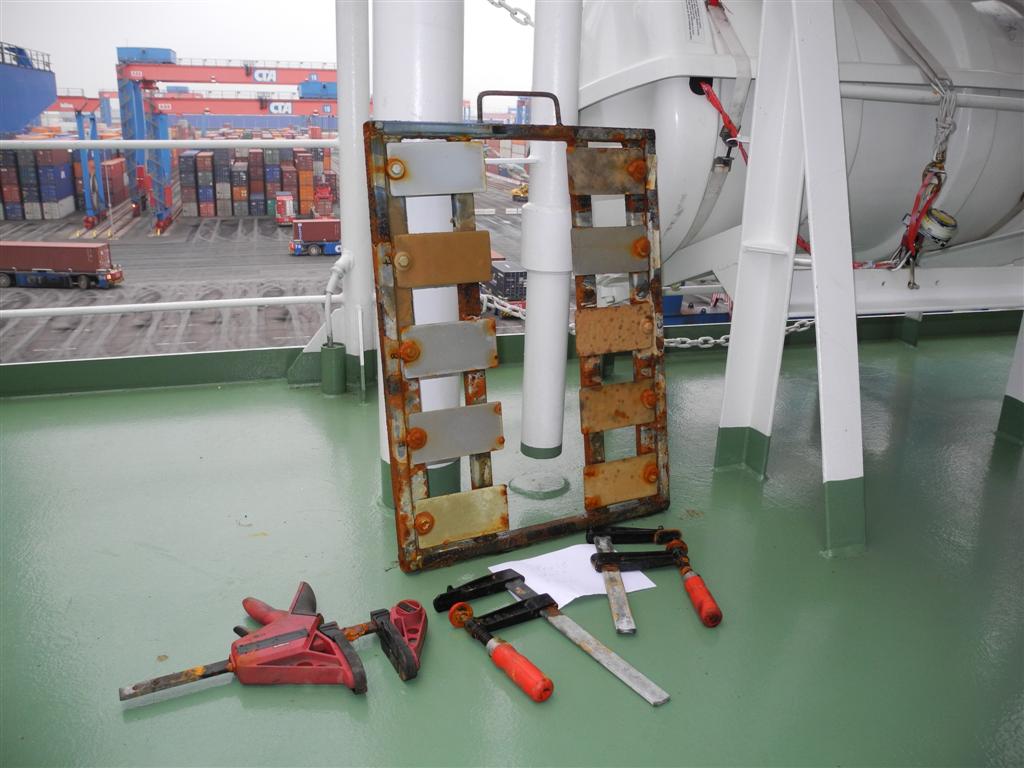
Damit die Prüfergebnisse gut sichtbar sind, ist unser Vorgehen immer gleich: Die neuen Produkte werden in vergleichsweise dünnen Schichten aufgetragen. Die Schwachstellen werden im Vergleich zum Referenzblech so relativ schnell erkannt.
Wichtig zu wissen: Viele der auf den ersten Blick sichtbaren brauen Rostflecken stammen von den Schichtdickenmessungen kurz nach dem Auftragen der Wachse. Bei den Messungen wurden die Schutzschichten bis aufs Blech weggekratzt. Die Schäden durch die Messungen werden bei der Auswertung nicht berücksichtigt.
Die Testergebnisse werden von uns wie immer auf andere Anwendungsbereiche übertragen. Nach der Auswertung der Ergebnisse war unser Chef Gerd Cordes sehr zufrieden. Wir wissen jetzt, wo wir eventuell nachbessern können und sind bei der Produktentwicklung wieder ein großes Stück weiter gekommen!
Im Dezember fahren wir für einen weiteren Test nochmals nach Helgoland. Auf unserem Testturm am Strand sind die Prüfbedingungen ähnlich extrem aber anders. Erschwerend kommt auf der Nordseeinsel noch Materialabtrag durch Starkregen und Salzwasser-Gischt hinzu. Eine weitere Erschwernis: Das UV-Licht hinzu. Die im Sonnenlicht enthaltene ultraviolette Strahlung bedeutet für Rostschutzprodukte zusätzlichen Stress. Die meist langkettigen Molekül-Ketten der Rostschutzprodukte werden durch die Sonneneinstrahlung relativ schnell “zerhakt”. Die Schutzschichten werden dann u. a. spröde und verlieren ihre Wirksamkeit. Ideale Prüfbedingungen also für einen Zeitraffertest, der auf andere Anwendungsbereiche übertragen werden soll.